Remote Welding refers to laser welding, where the laser beam is not guided by an operator or a robot, but by a galvanometric scanning head, following a path predetermined by software. The movement of the beam is precise, very fast, even on extremely complex paths.
More details…
Schematically, a laser light beam enters in the scanning head and is reflected by a pair of mirrors that, rotating on axes perpendicular to each other, move the beam in a plane at very high speeds, in all directions.
An F-THETA lens then focuses the laser beam on the working plane. The extension of the working plane depends on the focal length adopted.
This operating mode allows welding along predefined paths (a, b), with the following characteristics: – Process stability and repeatability – High mechanical strength – High productivity – Excellent aesthetic qualities – Full control over welding power distribution
An important feature of Remote Welding is the dynamic control of the weld bead shape and of strategy of weld, called wobble.The weld bead is created by a repeated, regular circular motion (c). In addition to the above-mentioned advantages, wobble allows the joining of parts with loose edges. Sisma welders with Remote Welding, thanks to full control of the laser beam, become so versatile as to allow processing other than just welding. This is the case for selective polishing of metals, achieving very varied and complex aesthetic effects (d).
For example, in the same texture (d), we see on the left the polishing carried out only on the bottom of the engraving, while on the right the polishing is limited to the top part; the result is a completely different aesthetic effect. Similarly, objects with complex shapes can be polished. This is achieved by melting a few tens of microns on the surface of the metal; there is no removal of material, so shape and size of the object are maintained.
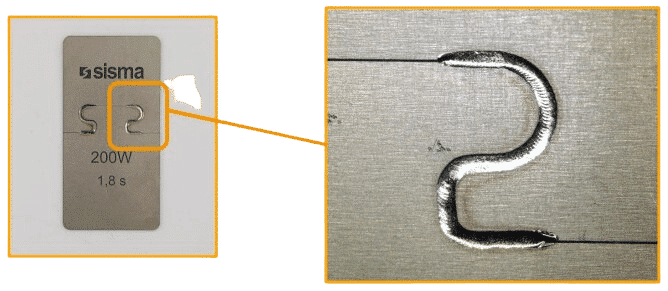
Picture A
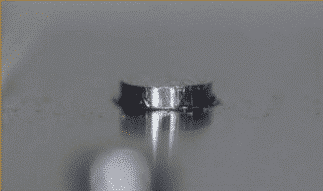
Picture B
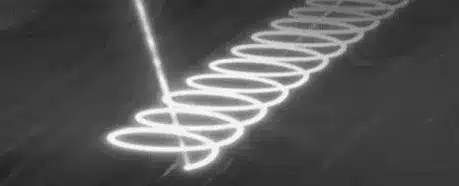
Picture C
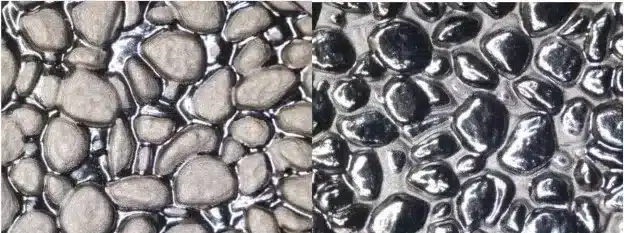
Picture D
CONTACT US
Oops! We could not locate your form.