UDI (Unique Device Identification) of medical devices
according to MDR and FDA and Sisma solutions
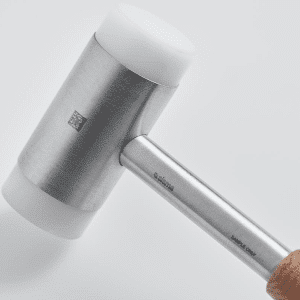
Courtesy of LUZ MEDIZINTECHNIK GmbH
Increasing patient safety through medical device identification
Patient safety is the first priority of both regulations and consistent labeling of each medical device is essential
to maintain traceability and transparency throughout the whole supply chain, from the MD (medical device)
manufacturer to the patient and across the entire product life cycle.
In 2013, the FDA (Food and Drug Administration) released the Unique Device Identification (UDI) of medical
devices directive. In 2017, the European Union narrowed the gap by implementing the Medical Device
Regulation (MDR). Both FDA and EU regulations have labelling and traceability requirements that differ for various MD risk classes. The labelling rules are likely to be implemented for all MD in any risk class in the next future.
UDI standards
UDI can be issued by accredited agencies in US (Health Industry Business Communications Council, International Council for Commonality in Blood Banking Application and GS1) or Notified bodies in EU.
Each MD (and it’s own packaging) will have a UDI composed of two parts: a device identifier (UDI–DI) specific to a device, and a production identifier (UDI–PI) to identify the unit producing the device.
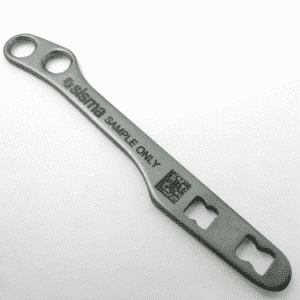
Titanium fixation plate with 2mm 2D UDI code
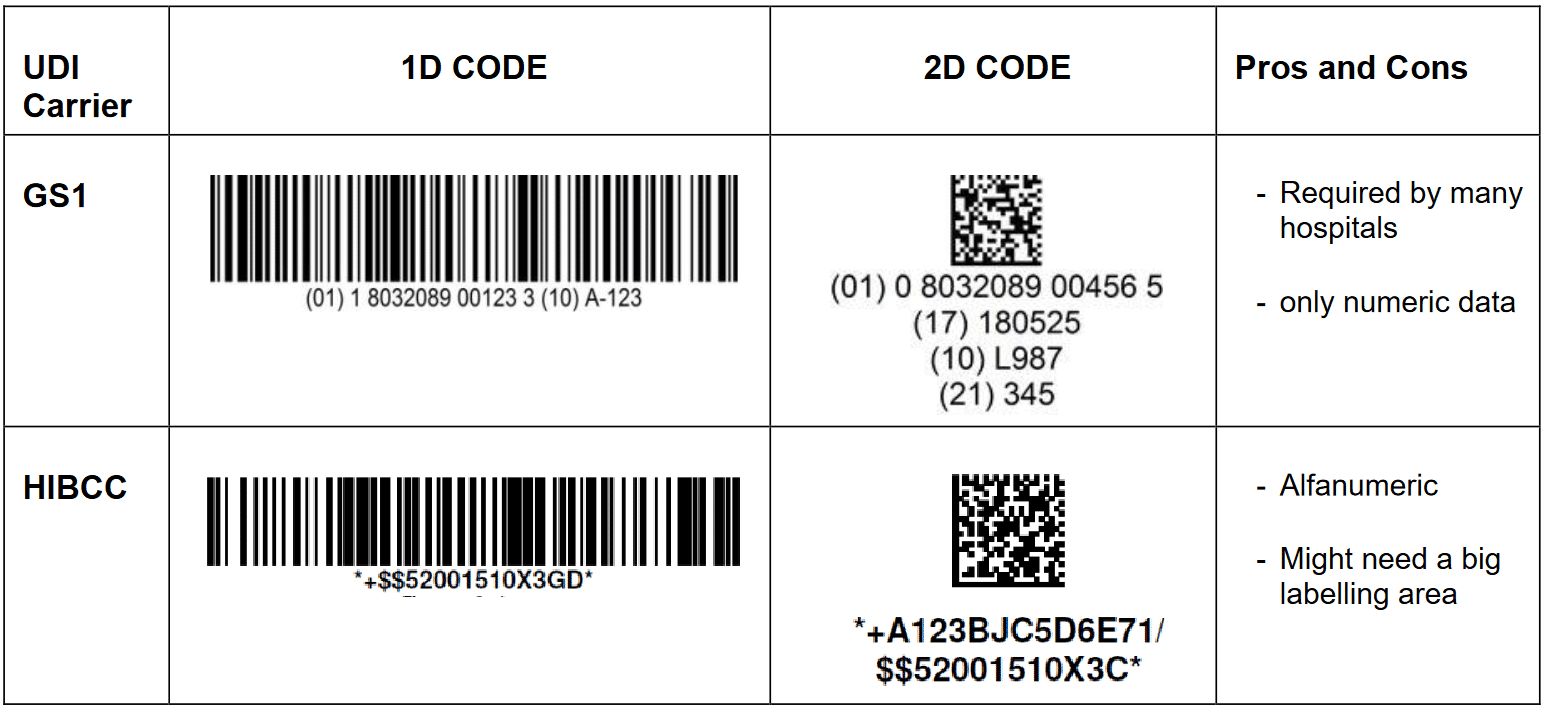
UDI can be applied as a 1D or 2D machine readable code and a human readable code. GS1 human readable code is particurlarly easy to read, having all the informations divided by headers:
(01) Device Identifier – (17) Expiration date – (10) Lot number – (21) Serial number.
Considering that many MD are rather small, a 2D machine readable code in the form of a datamatrix is a convenient choice since it can be miniaturized to 1mm and below.
Sisma turnkey solution for UDI medical marking
SLC3 control software for Sisma laser machines offers unique features to make UDI traceability marking easier and safer.
The UDI code is generated through manual or automated input, while the software constantly dialogues the company database via SQL queries. The software supports user levels with different authorizations; for instance, one user level is capable of setting up new projects while others can only recall existing ones and have limited or no access to process parameters.
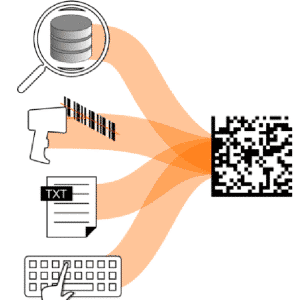
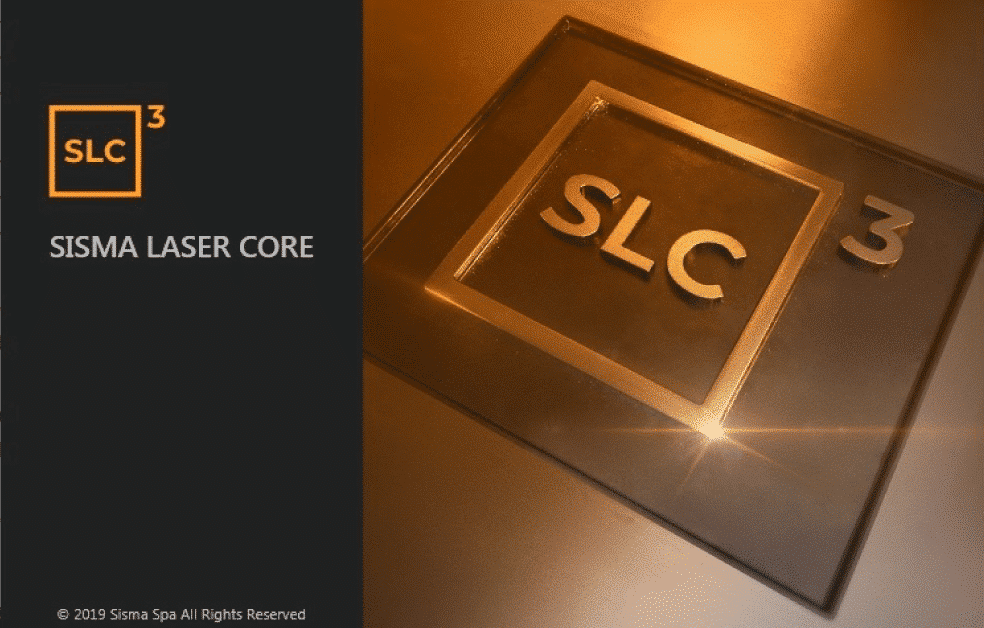
Four ways to load a UDI code
SLC3 marks UDI codes in either 1D or 2D data–matrix GS1 compliant format.
SLC3 recalls UDI codes to be marked in several ways:
– SQL query to the company database
– By scanning a barcode with a handheld reader from a printed job list
– Loading a third–party generated text file
– Typing the code on the keyboard
Assured marking repeatability thanks to
Thanks to CVS, Pattern Matching and server integration the machine takes care of:
– Auto Focus by moving the Z axis
– XY position and rotation of the marking thanks Pattern matching software (maximum error ±0.02mm )
– Marking the part in the correct position
– reporting to the internal database the marking results and correctness of the information
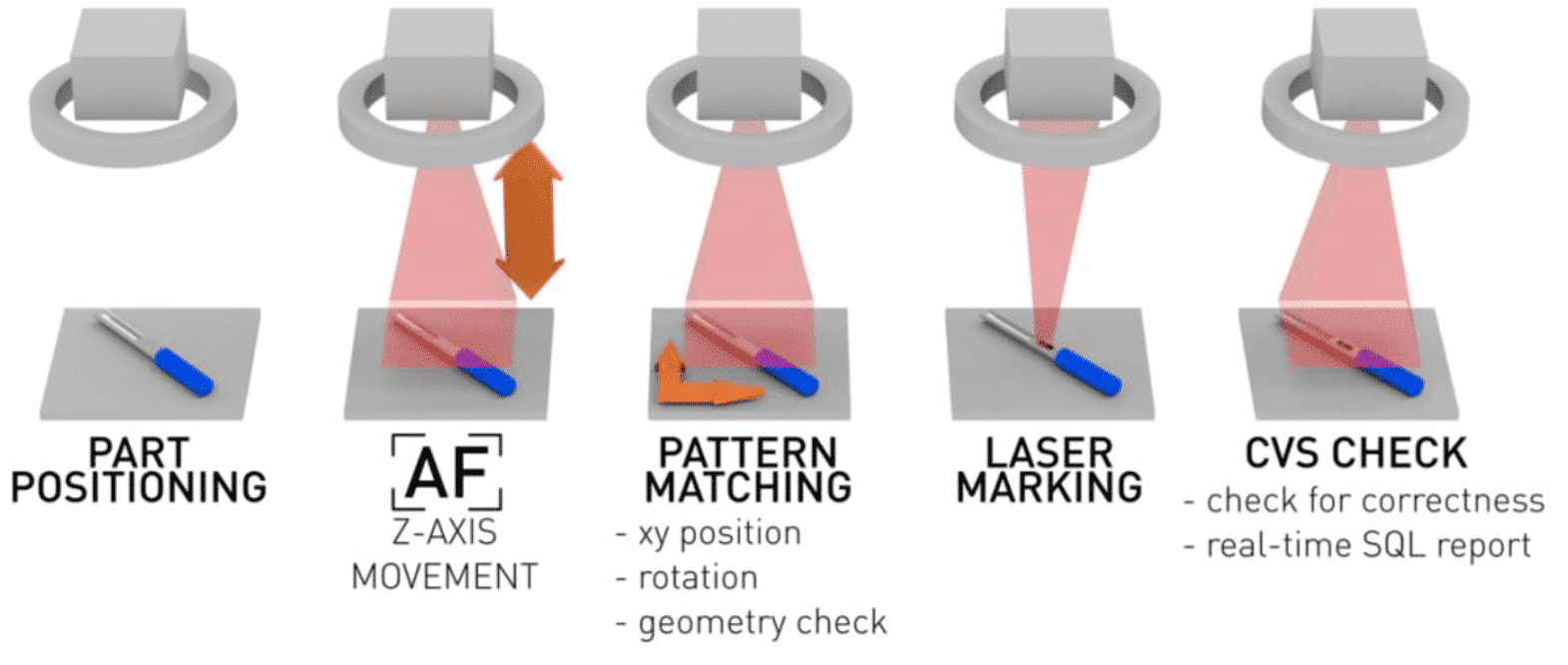
Sisma automatic loading solutions for high productivity
Process automation plays a huge role in the manufacturing of medical devices. Reducing errors and cycle time allows to reduce production costs and increase safety.
The SART platform, with dial rotating table, allows loading of the parts to be marked in masked time, representing an excellent solution for marking medium and large size components. The dial table can also be equipped with customized fixtures and accessories such as mandrels for marking cylindrical parts.
The BSP platform, available with MOPA nanosecond sources or Picosecond sources, can be ordered with WH10, an automatic loader of 10 fully customizable trays. The trays can have different number of pockets (depending on the size of the parts) and other options such as backlighting, that increases precision when acquiring complex shapes via CVS (Coaxial Vision System) and Pattern Matching.