Mechatronics
Mechatronics is the branch of automation engineering that studies the interaction of three areas: mechanics, electronics and information technology; it is an essential discipline for all industries, because it allows the efficiency and productivity of the work of men and women to be improved.
Applications of mechatronics are commonplace, especially in manufacturing and industrial automation, robotics, avionics, automatic mechanical systems in motor vehicles and all the various types of electrical drives.
This gave rise to mechatronic elements, by which we mean actuators (regulators, converters and energy transformers) that control motion; sensors, which detect the state variables of a process; and control devices (or regulators). The information included in these components must allow the identification and traceability of the part, and must be durable and easy to read despite the strain or wear to which they are subjected.
Laser marking in mechatronics
Laser marking, therefore, is essential to fulfil legislative obligations, traceability and warranty functions. Typical marking content ranges from Data Matrix codes for component traceability to alphanumeric characters and customised content.
Given its versatility, the laser is an excellent choice in all cases where it is necessary to carry out marking operations that require precision: this technology allows you to exploit the advantages deriving from a very small laser beam, from the possibility of modulating the process energy and the guarantee of obtaining a constant result.
However, when it comes to anodized aluminium, it involves removing the anodisation layer, obtaining an ideal contrast between the white background of the material and the colour of the coating. The aesthetic and functional performance is excellent.
While from a process point of view, laser marking is very simple, data management and the ability of the software or automation to automatically and safely show the necessary data are very important. For these reasons, Sisma offers its customers a dedicated range of specific products for this type of application, in order to guarantee the necessary reliability.
Bench marking systems, such as Easy or Big Smarky, are ideal in those situations where the user needs to mark labels but also to mark directly on the pieces. This is a hybrid use of the system and generally the quantities of pieces are small.
Plate machines
Laser technology is fundamental to all product traceability processes and applications. Among the most common and used, we find that relating to the marking of metal plates for products related to the world of pumps, electric motors, gearboxes and all those components that require immediate visibility of technical operating data.
This generally involves marking on steel or anodized aluminium plates. In the first case, deep engravings can be made in order to guarantee legibility in cases of wearing applications, or it is possible to create markings, blackened and impalpable, in order to have a top-level aesthetic result.
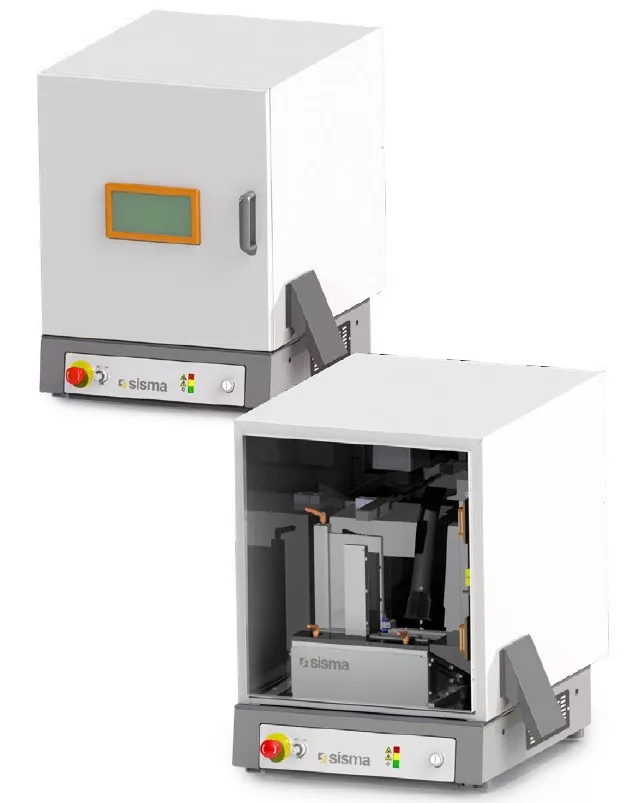
MP1
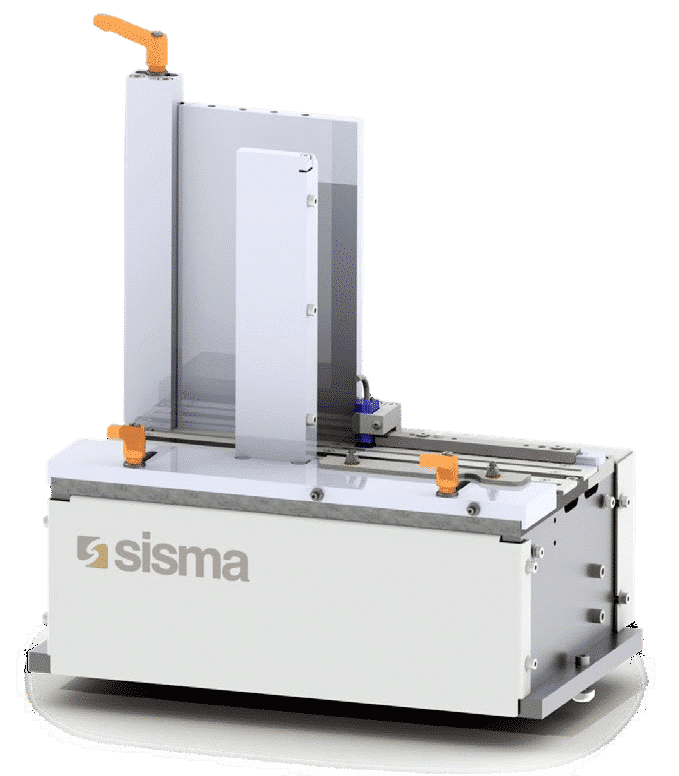
MP1B
However, if there is a need to only mark plates, the MP1 accessory is available which allows you to load up to 300 plates with a thickness of 0.5 mm, which are automatically “flicked through” and brought under the laser. The marked tags are then collected in a special container. This accessory can be mounted inside the Sisma markers or inside the MP1B module, a laser system dedicated exclusively to plate marking.
If the quantities of plates are large, Sisma makes the MPX system available. A laser system exclusively dedicated to laser marking of plates, ideal for large productions and great variability of formats. The system can accommodate up to 12 different plate formats which are automatically taken from the loading magazine and brought to the marking area. The plate can also be marked on both sides, if a further guarantee of traceability is necessary.
Once the marking has been made, it is possible to insert a barcode or datamatrix reading system in order to confirm the readability of the code and finally, it is possible to apply a protective film** if the plate, after marking and mounting on the piece, has to pass through a painting process.
Once marked, the plate is placed on an N-position unloading table; in fact, when large quantities are involved, it is necessary to divide the plates not only by format but also by batch. In this way, the operator will find the plates already automatically divided and will only have to remove them.
Infrared laser: quality marking for metallic materials
Infrared laser sources allow you to create indelible and very defined markings on most metal and plastic materials. These are very versatile lasers, in compact sizes, which essentially require no maintenance but have important performances in terms of reliability, precision and repeatability. They can be integrated within the entire range of solutions offered by Sisma: the product range is very wide, both in terms of available laser powers, in terms of size of the pieces to be marked and in terms of automation.
Among these, the LWS-A system stands out, a compact laser marking station that allows for a large load, thanks to the 3-axis gantry movement of the laser, which allows the positioning and marking of large quantities of pieces or multiple markings on a single large piece.
SART, laser marking and engraving system with rotary table
Sart is a laser marking system equipped with a two-position rotary table: the solution effectively responds to the demand for high productivity in the automotive sector, simultaneously guaranteeing maximum safety and the best ergonomics for the operator. The loading and unloading of the pieces takes place in masked time, on a table with a diameter of 700mm, with the protective partition that automatically raises and lowers, allowing high variability in the height of the pieces. Sart can be integrated with the dedicated robot interface, in order to guarantee all the functions necessary for the use of robotic automation systems, always safely.
Sart is modular and is available with infrared laser sources, from 20W to 100W power, CO2 and UV laser sources, capable of carrying out engraving, marking and micro-cutting processes on various materials. It is also compatible with the coaxial vision system (CVS), the Pattern Matching software and/or with the dynamic focus shifter function, for the creation of processes on complex non-flat surfaces.
UV laser: high contrast marking on plastic and non-metallic materials
The laser marking process can be performed with different types of lasers, based on the materials and the yield that the marking itself requires. The UV laser sources, integrated into the MODO or Sart systems, are designed for all high contrast marking and processing applications where aesthetic/chromatic rendering, definition of the laser line and productivity are essential requirements.
The UV lasers excel above all in marking plastic, glass and other heat-sensitive materials: the peculiarity is that they have a shorter wavelength than the most common traditional lasers that operate in the infrared, which is advantageous because it ensures a reduced laser, minimal thermal impact and the possibility of carrying out very high definition processing on plastic and/or organic materials, even on very small surfaces.
Easy with MOPA laser source or Q Switch
Traceability is essential in the manufacturing industry and ensures that all products are fully monitored at every stage of the supply chain: the Easy desktop laser marker with MOPA source, a technology of great precision and speed, is ideal for the marking of codes, qrcodes and all those identifying elements essential for the supply chain.
The ability to adjust the pulse width indirectly influences peak power, allowing MOPA laser systems to mark on a wide range of materials with high-contrast results and vibrant colours on stainless steel.
Laser welding technologiesin Mechatronics
Laser welding technologies are increasingly used throughout the mechatronics industry, in all those cases where precise, deformation-free joints are required.
It is possible to obtain weld geometries that can be parameterised according to the process and with minimal thermal invasiveness. Lasers weld both materials with a high melting temperature, such as steels, and materials with high thermal conductivity, such as various aluminium alloys.
SWT, sistema semi automatico di saldatura laser stampi
SWT is designed for the maintenance of small/medium-sized moulds of simpler stationary. The efficient laser welding machine is offered with Class I and Class IV laser systems which are intended for welding and moulds maintenance with and without filler material. You can easily set up adjustments height of the optic head on motorized function.
For intricate and tilting operation, you can also utilize XYZ magnetic locking vise with sufficient level of operator’s craftmanship. Laser parameters can be managed through intuitive touch screen that allows the control of the waveform, the diameter of welding and spindle rotation.
MODO with remote laser welding technology
The welding process is carried out with the aid of a galvanometric head; the motors that control the mirrors inside the scanning head move the laser beam within the perimeter circumscribed by the focal lens, with the advantage of process speed and ease of centring and programming.
Thanks to a rigid and modular structure, MODO weld guarantees high productivity while maintaining quality and repeatability of the welding process. The machine includes the CVS (Coaxial Vision System) vision system for viewing and easy centring of the piece which can be combined with the PM (Pattern Matching) software for automatic component recognition.
SWS, 3 or 4 axis CNC automatic laser welding station
SWS is the automatic CNC welding station with 3 or 4 interpolated axes controlled by CNC, with self-learning or ISO path. The axis movement system, with recirculating balls, guarantees high precision thanks also to the solidity of the structure and the materials used. In this case, the welding head follows a previously created tool path, moving in the work chamber depending on the size of the piece and the required equipment.
The laser source has been designed to guarantee high operating stability at both low and high power; the fibre technology allows to obtain a reduced size of the beam diameter combined with high stability, both in initial transients and for demanding uses.
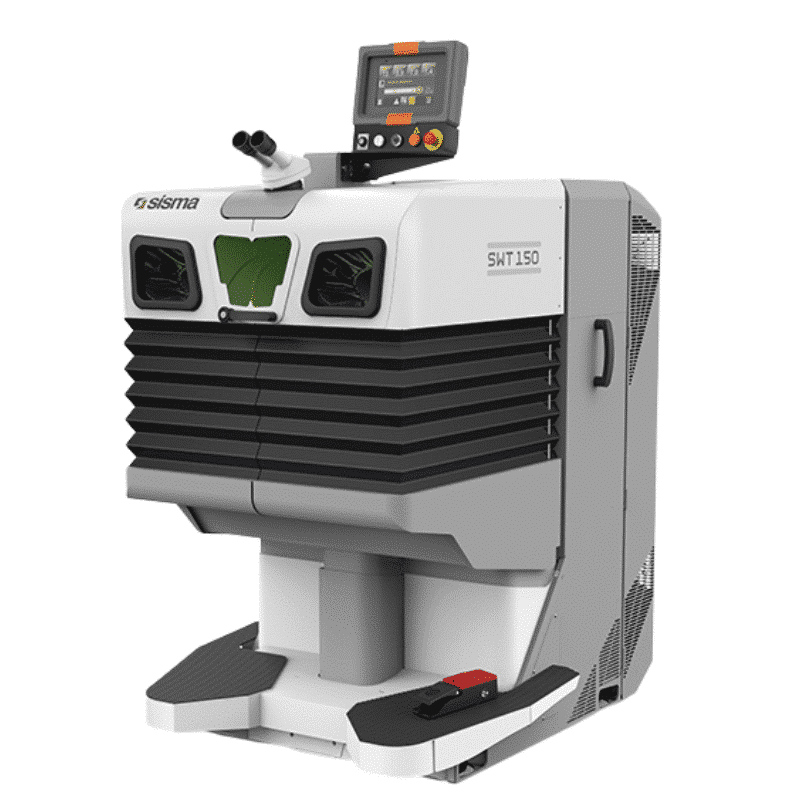
LM-C, the automatic laser welding system ideal for repairing small moulds
LM-C is an automatic laser welding system ideal for repairing small moulds. Thanks to advanced software and laser functionality, including a CNC, the system autonomously handles circular profiles, linear sections and automatic fills through a weld path.
With the LM-C and a special swivel optic, a medium-sized workpiece can be welded horizontally on the workbench.